The laser guided AGV system is a high-tech integration of light, machine, electricity, and computer. It is a flexible and highly intelligent conveyor system with a wide range of applications.
In the application of the AGV system, the operation mode and quantity of the AGV must first be determined according to the overall requirements of the system.
The operation mode of AGV should be specifically designed according to the actual number of systems and user needs. The usual operation modes are: rail type, forklift type, side fork type, traction type, etc. In special circumstances, the same system can be used in different AGVs. Different operation methods are used on the above, and the number of AGVs can be determined according to the transportation capacity required by the system and through simulation results.
1. AGV safety protection
On the AGV, in addition to sound and light alarms and mechanical anti-collision baffles, non-contact obstacle detectors are also installed to detect obstacles on the driving path. The general forms are: photoelectric detection, ultrasonic detection, Laser scanning detection, etc. Among them, laser scanning detection has the highest reliability and intelligence, but the cost is too high, and photoelectric detection is the simplest and easy to use, but there may be "blind areas" that cannot be detected. Therefore, it should be specifically selected according to the environment in which the AGV operates.
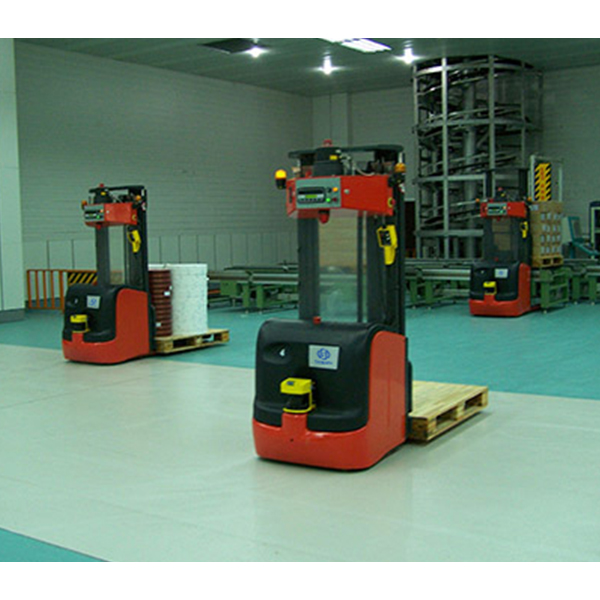
2. AGV communication
The "wireless digital communication" is adopted in the laser guided AGV system, and the frequency band of the communication should be selected according to relevant national regulations. The communication between each AGV trolley and the system is carried out in "round-robin". The baud rate (communication speed) of the wireless modem determines the speed of the "round-robin" communication, thus limiting the maximum number of AGV cars that can be controlled in this frequency band. Quantity.
3. AGV system monitoring
The operator can monitor the running status of the AGV at any time through the monitoring computer, such as walking, parking, loading and unloading, etc., and can intuitively see the operating area of each AGV trolley. When an unexpected failure occurs in the operation of the trolley, the current command can be manually cancelled and the system problem can be solved.
4. AGV automatic charging,
Each AGV can measure the current capacity of its own battery at any time. When the battery capacity drops to a low limit, it will send a charging demand signal to the system, and the system will issue a charging command to the AGV. When the AGV arrives at the charging station, the system controls the ground charging equipment through the I/O interface to charge it. After being fully charged, the charging demand signal disappears, and the AGV car can continue to accept other tasks.